Produced water recycling is a rapidly evolving market with growing pressures. Several factors are driving market growth, including freshwater scarcity, an increasingly favorable regulatory environment, and societal concerns about seismic effects of disposal injection.
Together, these forces are creating a major opportunity for recycling produced water. According to the American Oil & Gas Reporter, the Permian alone is projected to recycle >6M bbl of produced water each day by 2030 (Figure 1).
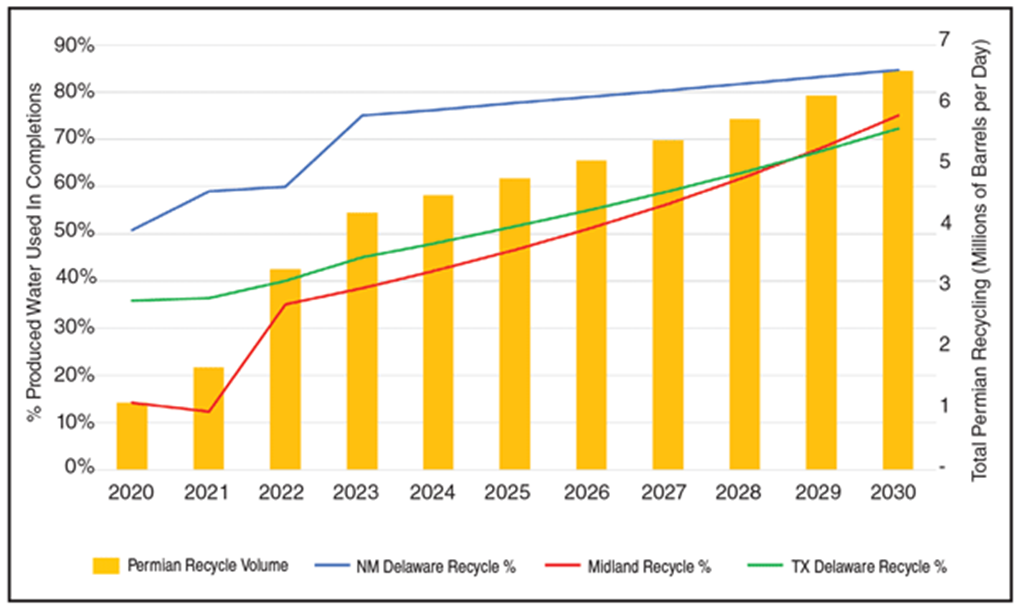
Attractive economics of recycled water compared to freshwater alternatives is an important factor in driving adoption. This means competitive pricing is key, yet inconsistent water quality can create a cost challenge for water recyclers. Current treatment chemistries are insufficient to handle the wide variety of incoming water types while maintaining maximum system throughput. The resulting inefficiencies and extra spend inhibit recyclers’ ability to maximize throughput and value.
The Problem
A Solugen customer was combatting several problems as a result of poor water quality:
- Highly variable water feeding into facility was frequently exceeding KPIs for iron, TSS, and residual oil
- High solids content was building up in filters
- Lost opportunity to treat incoming waters
- Incumbent chemical program of H2O2, FeCl3 and PAM polymer marginally effective
These issues caused by high water variability and solids were negatively affecting water quality and throughput. Initial lab testing with adding 10 ppm of Verza360 XT, Solugen’s organic acid-based additive, demonstrated both improved oil- and solid-liquid separation and water clarity.
With these promising results in hand, the customer moved to conduct a large-scale field trial. A team of Solugen representatives from technical business development, product management, and product development joined on-site to support the trial. They offered technical guidance and answered customer questions along the way.
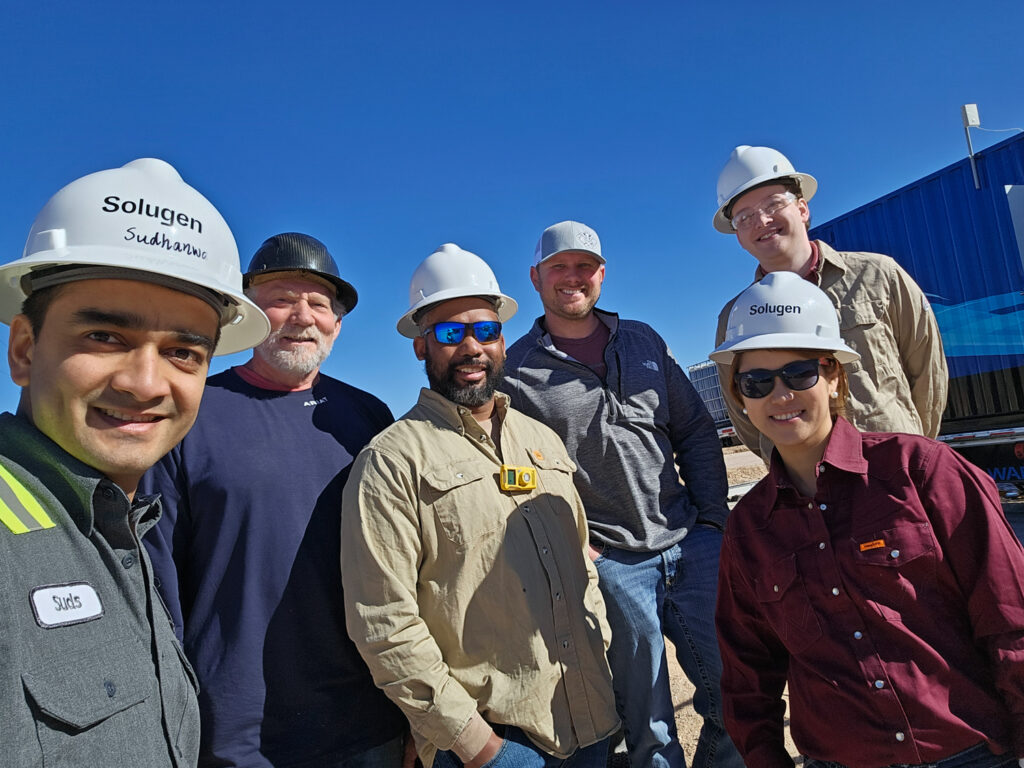
The Results
Solugen’s chemistry enabled larger and tighter layers of flocculant, facilitating faster and more effective oil- and solid-water phase separation. Applying 10 ppm of Verza360 to the customer’s incumbent program demonstrated multiple improvements. The team saw immediate improvement in treatment KPIs per Table 1. Notable results included a 30% increase in flow rate across the filters, >50% dP reduction across filters, and >40% reduction in iron and turbidity.
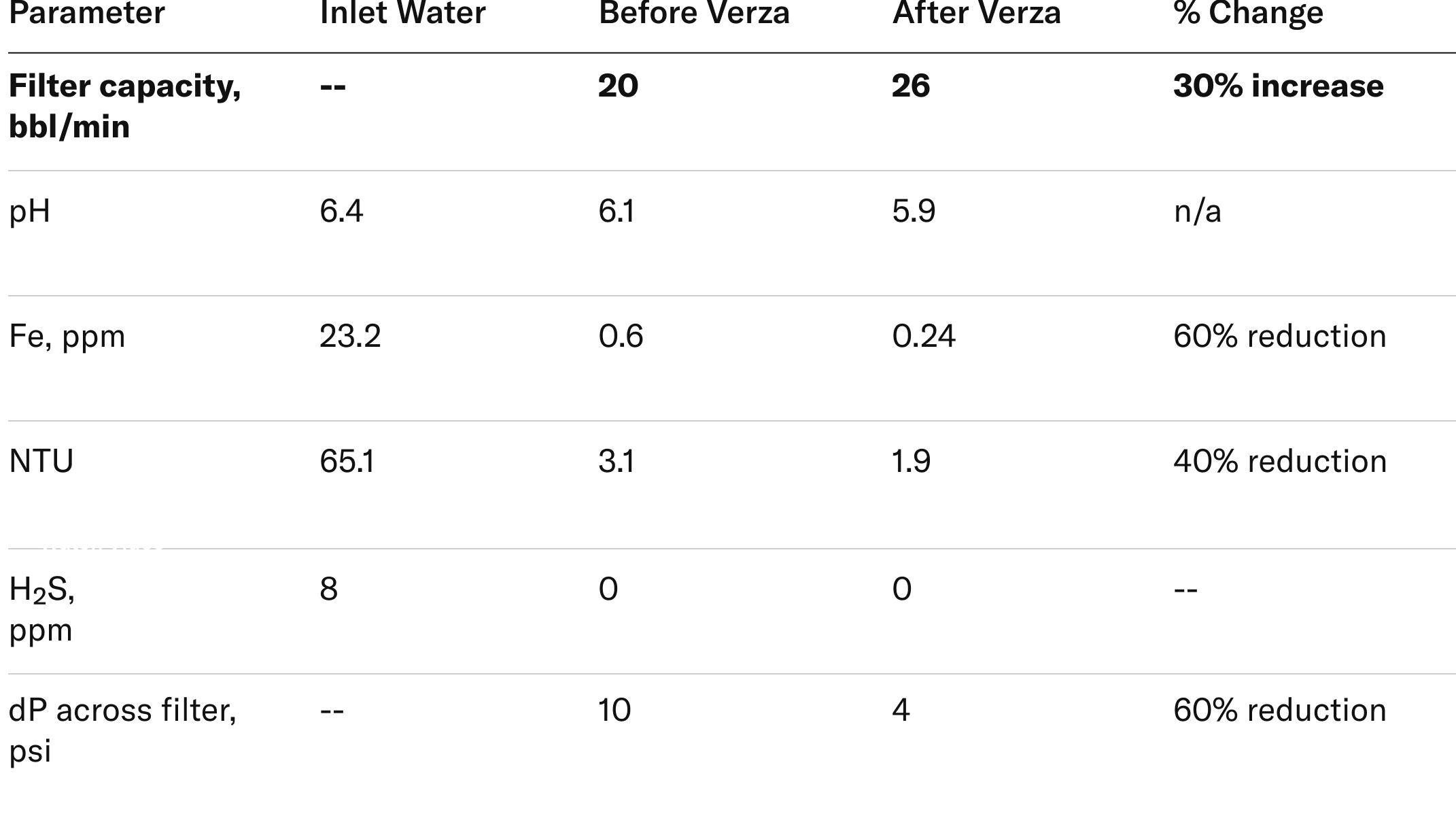
Further, as shown in Figures 3 and 4, the team saw improved flocculation, oil- and solid-water phase separation, thereby making it easier to skim these layers off the top.
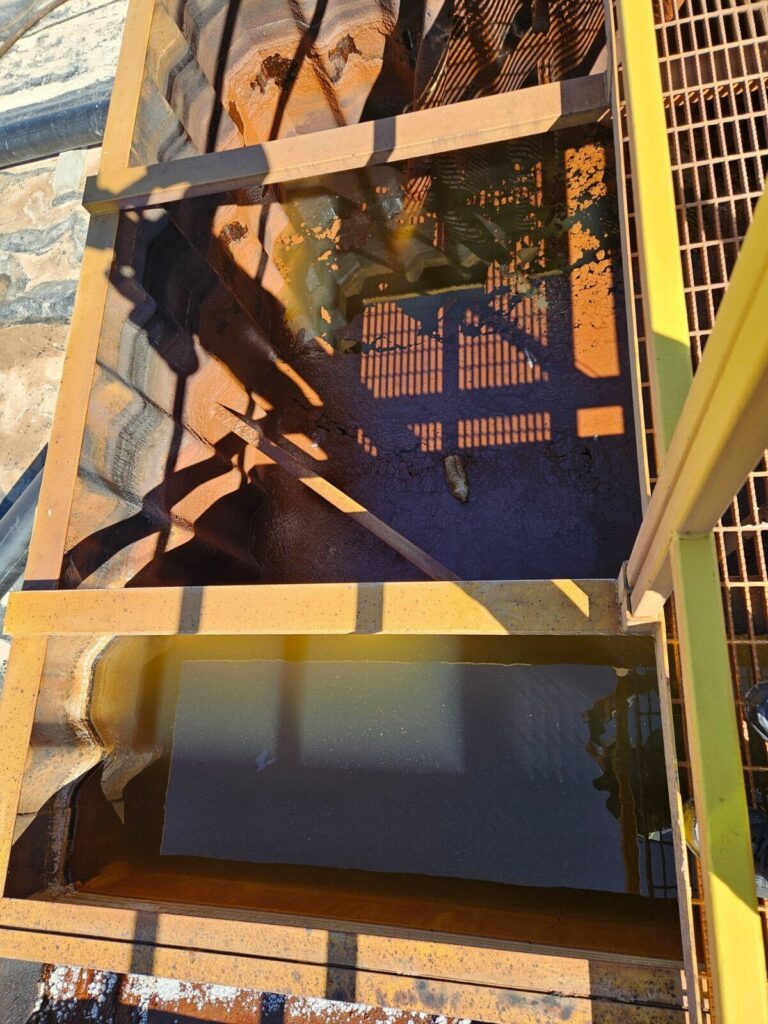
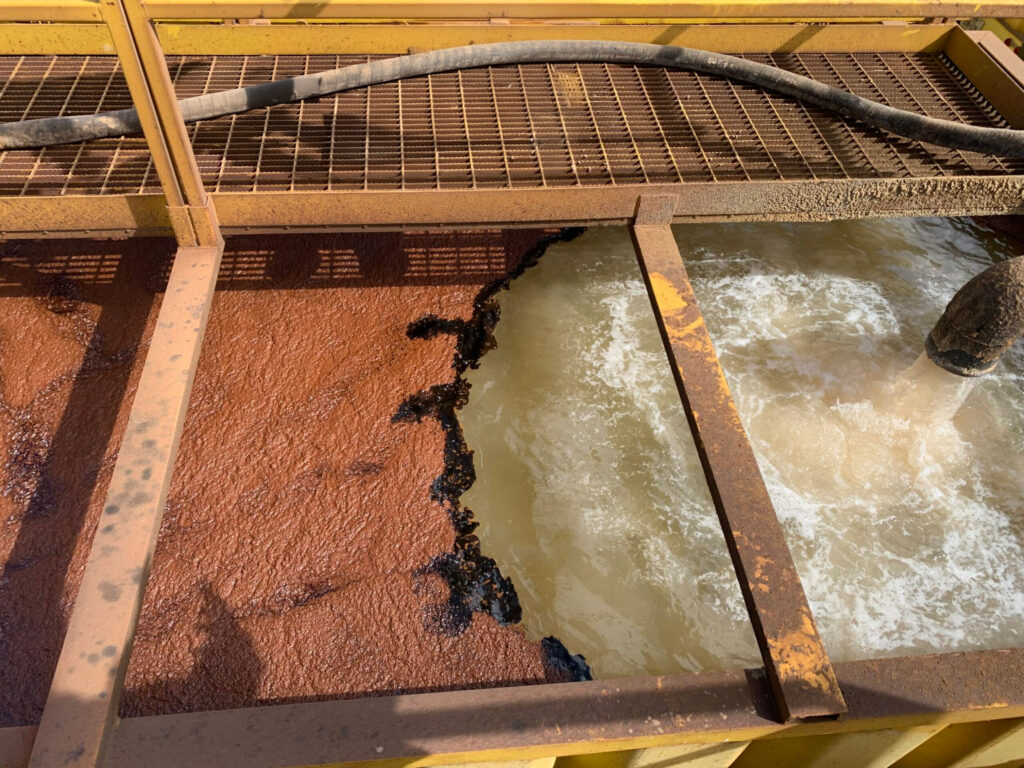
The trial demonstrated overall that adding Verza360 increased the ability to handle more contaminated water and consistently achieve a steady-state operation. This improved productivity helps recyclers achieve several chemical and operational savings per barrel, including:
- Reduction in re-treating internal water
- Less chemical overfeeding to reach KPIs
- Decrease in cost required to skim tanks and replace plugged filters
Why Verza360?
Adding Verza360 to a produced water recycling program can positively impact both performance and cost. The product’s compatibility with all commonly used existing flocculant, coagulant, and oxidizer chemistries means it can be easily added to a treatment program, but actually reduce the overall chemical and operational spend thanks to resulting performance gains. More water treated with a better economic profile means produced water recyclers can capitalize on this growing market.
To learn more, please contact us at energysolutions@solugen.com or visit www.solugen.com/oilandgas.